Suppose your next construction project ranges from a single-family home renovation to complex urban multi-use developments. In that case, you must also consider procurement as an integral part of the project’s overall success. For construction industry folks, it is really not about just finding suitable material or scheduling; instead, it is about the bottom line of making money. Improper workflow management usually results in broken project data and can let inefficiencies into your system, also referred to as Gray Work, that slow down the processing time.
How procurement teams are structured and what technology is used to run the procurement process can significantly alter the total cost of delivering a construction project. This piece aims to walk you through the different procurement methods in construction and some best practices to enable you to choose the best solution for your company, to help you optimize operations, save costs, and deliver better project results.
Table of Contents
What Is the Construction Procurement Process?
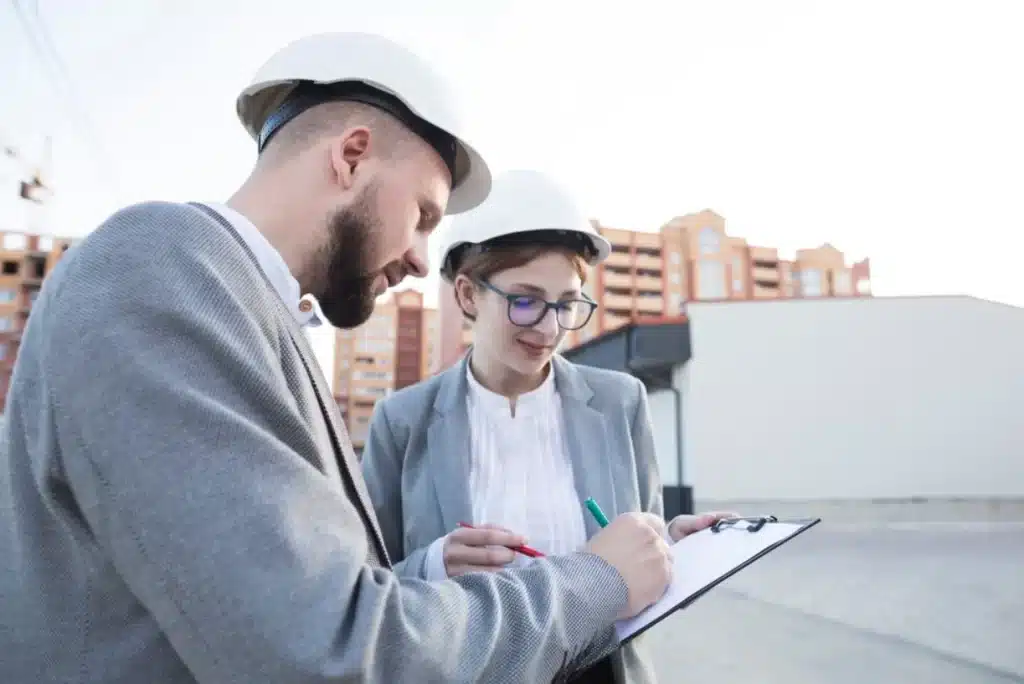
In construction, the products and services needed to finish a project on time and within budget are strategically acquired through procurement. A project manager usually oversees this process, which involves five key responsibilities:
- Determine project needs.
- Request and review proposals for services.
- Buy or lease needed materials, tools, and equipment.
- Manage construction contracts and proactively handle emerging costs and schedules.
- Manage and resolve budget, timeline, quality, and other issues.
Having the right plan and tools in place is essential if you want to enable high-quality materials and services to be available at the point of use when needed in a procurement process that is executed well.
The Benefits of Construction Project Procurement
Extremely important and what is more, a highly skilled procurement process is an ideal construction process that guarantees successful implementation of each building project, starting from the concept stage and ending up with its final stages in terms of construction timelines and, of course, funding. As these targets are usually set on an organizational level, companies grant bonuses to groups that achieve them.
For smooth operations, a comprehensive and user-friendly procurement system is essential. Disconnected systems can cause errors, costly change orders, and budget overruns.
Effective procurement solutions are accessible to companies of all sizes. An ideal system features an intuitive dashboard and capabilities such as:
- Consolidating schedules into one timeline.
- Efficient contract sharing.
- Managing change orders.
- Conducting cost analysis.
Discover this building solution for simplifying procedures, guaranteeing adherence, minimizing hazards, handling timeline adjustments, keeping within financial limits, and improving immediate team interaction.
Who Is Responsible for Procurement in Construction Management?
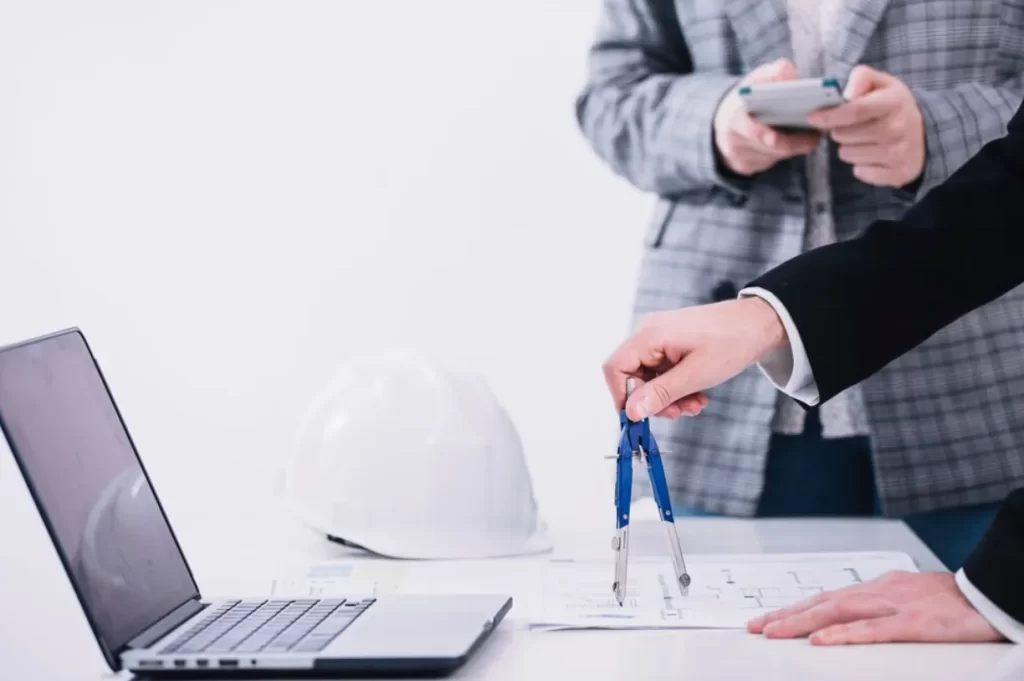
Most experienced contractors have a dedicated procurement manager to oversee construction procurement. This individual or team leads logistics, overseeing bidding, purchasing, scheduling, budgeting, and employee compensation. The role of a procurement manager varies depending on the company size and project scope, but at a minimum, they:
Create a Strategic Procurement Plan
While many companies have a procurement plan, unexpected challenges often arise during projects. Therefore, the procurement manager must stay focused on the goal and be ready to adjust to changes in deliveries, scope, or schedules by incorporating backup systems and extra time into the construction timeline. Contingency planning is essential, especially during supply disruptions. A strategic approach from the outset enables procurement managers to handle multiple setbacks while still achieving satisfactory outcomes.
Evaluate Contracts, Requests for Proposal, and Bidding
Posting, responding to, and winning RFPs, as well as writing and managing contracts, consume most of the time for procurement managers. These proposals should be scrutinized at a time when construction has recently become a harsh industry for many businesses, with worker shortages and supply-chain issues. Moreover, ways of reporting like that of Environmental, Social, and Governance (ESG) report an extra take for projects and thus ask for a thorough assessment before taking any action.
Manage Resources and Schedules
The procurement manager is responsible for developing and maintaining detailed schedules for both personnel and materials. The primary objective is to ensure the workforce has everything needed to keep the project moving. Technology can aid in managing these schedules, allowing for an adaptable construction timeline that can accommodate delays in materials or construction progress.
The critical aspect of the construction procurement process is monitoring. Real-time visibility allows managers to adjust schedules and address project delays effectively and quickly. This proactive approach provides the necessary time to develop solutions and keep the project on track.
Types of Procurement in Construction
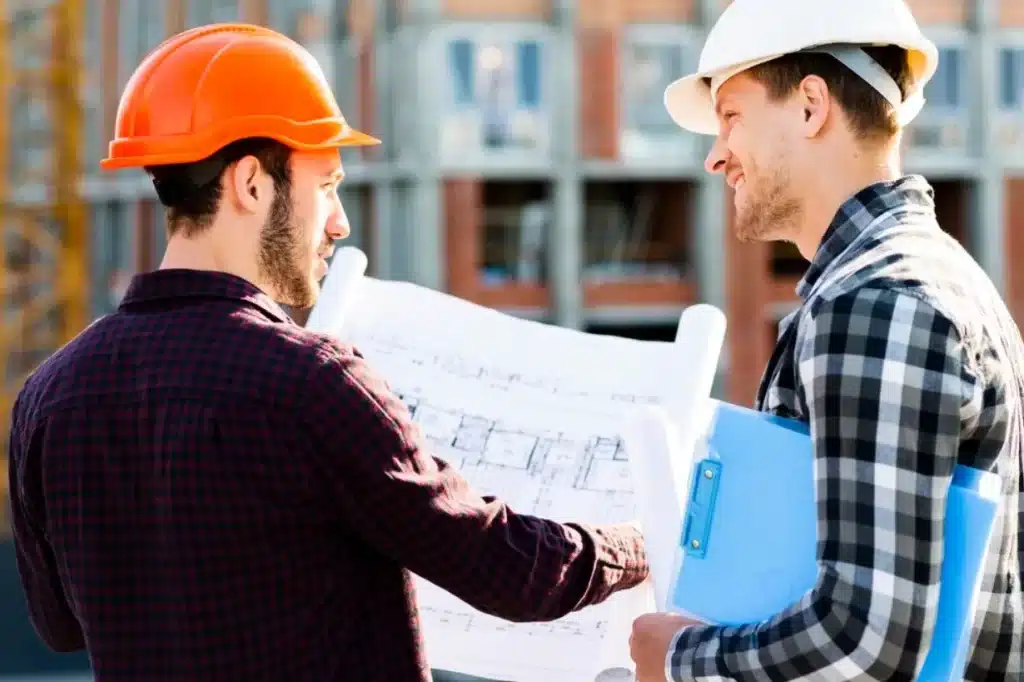
While numerous procurement methods are available, companies seeking expedited, high-quality work within budget constraints must carefully evaluate their options. Key factors to consider include:
- Cost
- Budget
- Financing terms
- Quality
- Speed
- Risk tolerance
Here is an overview of the main types of procurement for construction services:
Design-Bid-Build (Traditional Contract)
Design-Bid-Build is the contractual arrangement through which an owner procures a construction project, and this is carried out as described below: After the design phase is complete, they re-tender the project to have different contractors come in and put in a bid. Once the general contractor is hired through a fixed fee structure, he is accountable and directly involved in signing the construction contract, which involves supervising subcontractors and the actual construction process. The contractor exists to ensure the project is implemented on the proper schedule and at the correct cost.
A benefit of this method is that the owner typically warrants the design documents, meaning any design errors are resolved between the owner and the architect, with associated costs covered by them. However, a downside is that the design is developed without the construction contractor’s input, so opportunities for value engineering are missed in the initial design phase.
Design and Build
In construction, projects are typically procured through five methods: general contractor, design and build, construction management, joint venture, and private finance. Each method has its pros and cons, suiting them for specific types of projects.
Management Contracting
In a Management Contract setup, multiple contractors handle different functions for a fixed fee, typically a percentage of the total project cost. This method is frequently employed for large-scale projects. One contractor, designated as the Managing Contractor, is responsible for overseeing the design, construction documents, and overall project management. This lead contractor earns a higher fee than the others but also takes on greater responsibility and accountability.
Construction Management
This method resembles a Management Contract but with a notable distinction: the owner hires a management team to oversee the procurement process for a fee instead of directly engaging with other contractors. A vital benefit of this approach can be seen in large commercial projects where several drywall companies are contracted due to the high volume of work. If one contractor falls behind, another can step in to maintain the project timeline.
Private Financing
A contractor who is financially strong, large enough, and experienced at their job can use their credit and knowledge in this case. The contractor manufactures and carries out the design and construction of a facility or complex and then leases it to the client for a specified duration of time. It is best for Clients with a project deadline or tight timeline who need their final project fast but lack the short-term capital required to build and implement from the ground up.
Innovative Approaches
Construction procurement is poised for some significant change, and the more complex and innovative methods are showing promising signs. The primary method being used is called Progressive Design-Build, which moves the contractor into the design stage earlier than the traditional Design-Build model. Moreover, public-private partnerships can provide a mix of a Design-Build with different procurement, operations, maintenance, and financial models.
Also, the approach has developed at an incredible pace, and integrated project delivery seems to be becoming popular and growing widely. This way of working promotes increased cooperation among the designer, the builder, and other stakeholders in the design and construction process, as they share both the risks and rewards.
Frequently Asked Questions for Construction Procurement
What are the procedures of construction procurement?
In construction, the primary procurement routes include the general contractor system, design and build, construction management, joint ventures, and the private finance initiative. And it is specific in terms of the benefits and the options as well as the kinds of tasks that are good for this sort of strategy.
What does procurement in the construction sector entail?
In construction, procurement involves obtaining all necessary materials and items for a particular project. This includes buying items like raw materials, workers, equipment, machinery, and other essential goods and services for manufacturing.
What Is a Construction Procurement Strategy?
A construction procurement strategy is, therefore, a plan and organizational model that establishes the process to be used in acquiring products and services. This strategy focuses on the tendering process and procurement contracts to enhance how they are obtained efficiently.
How Does Purchasing Differ from Procurement in Construction?
While purchasing is more a cost reduction activity for the purchasing of materials or services per order, procurement is an overall and complete tender and supplier management effort that concentrates on the overall tender costs of using materials or services, the management of the supplier relationship, and the compliance with agreed-upon contracts.
What Is a Construction Purchase?
Consequently, the construction purchase is the acquisition by the construction agent of the facility and its ground interest as stipulated under Article XI of the Participation Agreement.